Technical introduction
This machine is a kind of flow continous drier. It is used to drying chip, strip and granular materials which have good air permeability. It is especially applied to drying materials with high moisture content, such as vegetabels and medicines which can not afford high temperature. This series of drier holds advantages of fast drying, strong evaporation and good quality. It can also be applied to drying dehydrated filter cake shape paste materials which need to be pelletized and be made into rodlike things.
Advantages
Can adjust air amount, heating temperature, staying time of materials and feeding speed in order to get best drying effect;
2. Flexible configuration; can use mesh washing system and material cooling system;
3. Flexible operation; after entering the drier, wet materials will be dried in a totally closed box, which avoids the emission of dust; save labor force;
4. When materials move along the conveying belt, the relavant position between materials is fixed. The drying time is almost the same. This machine is suitable for some drying processes where uniform change of color and moisture content are requested. What’s more, materials get slight vibration and shock in the equipment. It is difficult to crush these materials. As a result, it is also suitable for materials which permitting no crushing;
5. It can not only dry materials, but also can bake, ripen and cool the materials;
6. Special air distribution device makes even air distribution and grantees consistency of products;
7. Simple structure; easy installation; can be operated for a long time; workers can enter the inner part to check while there is malfunction; easy maintenance;
Working principle
Materials are evenly distributed on the meshes by feeder; meshes always adopt 10 to 60-mesh stainless steel screens which move in the drier dragged by drive device. Drier is made of many parts. Hot air in each part circulates independently. Part of tail gas is discharged by special wet exhaust fan. Exhaust air is controlled by adjustment valve. Hot air passes through meshes which covered by materials from top to down or vise versa to finish heat and mass transfer. The moisture content can be eliminated. Meshes move slowly. The moving speed can be adjusted according freely according to material’s temperature. After being dried, materials drop into material collector constantly. Up and down cycle unit can be flexibly equipped according to customers’ demands. The number of units can be chosen according to customers’ demands.
Structure chart
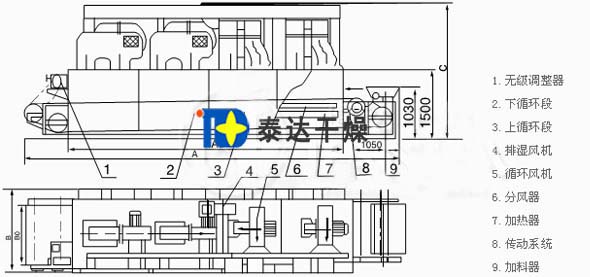
Technical parameters
Models |
DW-1.2-8 |
DW-1.2-10 |
DW-1.6-8 |
DW-1.6-10 |
DW-2-8 |
DW-2-10 |
DW-2-20 |
Units |
4 |
5 |
4 |
5 |
4 |
5 |
10 |
Width of belt(m) |
1.2 |
1.6 |
2 |
Length of drying stage(m) |
8 |
10 |
8 |
10 |
8 |
10 |
20 |
Thickness of distributed materials(mm) |
10-80 |
Operating temperature(oC) |
50-140 |
Steam pressure(MPa) |
0.2-0.8 |
Steam consumption (kg/h) |
120-300 |
150-375 |
150-400 |
180-500 |
180-500 |
225-600 |
450-1200 |
Drying time (h) |
0.2-1.2 |
1.25-1.5 |
0.2-1.2 |
0.25-1.5 |
0.2-1.2 |
0.25-1.5 |
0.5-3 |
Drying capacity kg/h |
60-160 |
80-200 |
85-220 |
100-260 |
100-260 |
120-300 |
240-600 |
Total power of equipment (kw) |
11.4 |
13.6 |
14.6 |
18.7 |
19.7 |
24.5 |
51 |
|
Length(m) |
9.56 |
11.56 |
9.56 |
11.56 |
9.56 |
11.56 |
21.56 |
Overall dimension |
Width(m) |
1.49 |
1.49 |
1.9 |
1.9 |
2.32 |
2.32 |
2.32 |
|
Height(m) |
2.3 |
2.3 |
2.4 |
2.4 |
2.5 |
2.5 |
2.5 |
Total weight kg |
4500 |
5600 |
5300 |
6400 |
6200 |
7500 |
14000 |