Technical introduction
Double stage coal gasifier is featured in following advantages:
1. Less pollution: coal gas from lower section of double stage coal gasifier is produced from gasification and dry distillation. There is almost no tar contained in the coal gas. Therefore, coal gas from lower section can be cooled indirectly (air cooler and indirect cooler) after shock cooling, which avoid sewage produced by direct contact between water and coal gas and prevent sewage pollution. Shock water cooling system is lacking of water. There will be no sewage discharge out. Water circulation usage can be improved after sedimentation. Disposal is very simple.
2. Both gasification strength and comprehensive efficiency are higher than single stage coal gasifier. It can be applied to wide range of coal. All coal gas produed adopt closed cycle. No sewage and air pullution. Water saving effect is obvious. It is a environment friendly and low cost equipment.
3. With proper height and structure dry distiller section, coal will be gradually heated during the dry distilling. Under low temperature distilling process, tar produced will not be cracked, with low stickiness and good flowability.
4. Tar produced in top section of coal gasifier is mainly light tar and with low dust content. After disposal by electricial precipitator, coal gas will almost not be blocked during long-distance transportation.
Structure advantages:
Coal feeding section: with reliable coal level gauge which works with coal charger to finish coal feeding work so that to make sure full coal level work condition.
Dry distilling section: with lining. System is desiged after precise heat transferring and heat exchanging. Heat transfer efficieency is improved. Coal to be gasified will be fully dried and distilled so that to precipitate volatile matters and improve calorific value of coal gas. It is beneficial for gasification of coal gas at lower section.
Gasification section: adopt water jacket structure, self-produced steam will be for gasification at furnace bottom.
Coal charging device: adopt advanced bell coal charging device, featured in simple operation, easy maintenance and good seal effect.
Ash cleaning device: adopt hydraulic driving ash cleaning device. large knife adopts self-designed colt type ash removing knife which makes sure stable transmission and smooth ash cleaning. Our plough type ash cleaning device has been widely applied in coal gasifier and enjoys great polularity.
Advantages
Coal gasifier is divided into two kinds, single-stage and double-stage. Double-stage coal gasifier can also be called two-stage coal gasifier. Furnace body of double-stage coal gasifier can be divided into two parts, upper part and lower part. Raw materials are sent to upper part of coal gasifier by bucket elevator and the materials are distilled. Then, semi-coke is formed. The whole process for coal gas production is finished in coal gasifier. Coal gasifier is specially designed for gasifying bitumite. It has many advantages of high thermal value, environmental protection, large amount of by-product tar and good quality of jar. The coal gasifier developed by our company is characterized by good heat transfer effect, complete distillation, easy structure and convenient maintenance.
Advantages of double-stage coal gasifier:
1. Less pollution: coal gas at lower section is got from coke after pneumatolysis and distillation. There is almost no jar contained in coal gas, which makes coal gas at lower sections of coal gasifier cooled down after extreme cold. Large amount of sewage caused by direct contact between water and coal gas is avoided. Then, sewage discharge will be avoided and no pollution is caused to environment. Because quench water system is deficient in water, there is no sewage discharged out. Water recycling use can be improved by settlement treatment. It is easy to dispose.
2. Gasification intensity and comprehensive efficiency are higher than single-stage coal gasifier; can adapt to various coals, especially bitumite. Closed circuit is adopted for coal production in coal gas station. No sewage and air pollution is caused to environment. It saves a lot of water resources. With advantage of environmental protection, it holds much less running cost.
3. Owing to a distillation section added in double-stage coal gasifier, coal is heated gradually in distillation part and distilled with low temperature. All tar produced will not be decomposed. The stickiness of tar is low and with good fluidity.
4. Tar produced in upper coal gasifier is mainly light tar; less dust brought out; coal gas is purified by electric light and electric catching focal treatment.
Working principle
Process flow of double-stage thermal desorption gas station:
Upper coal gas enters into electric filter whose working temperature is from 100 to 150 degree centigrade. After being polarized, tar mist and dust in the gas come together into a polar tube war and flow to tar tank. After passing through ash bucket, big granular dust will enter cyclone dust collector for being centrifugal dedusting. The temperature of dedust coal gas is from 500 to 600 degree centigrade. After mixing, coal gas at lower part and upper part will enter heat furnace through conveying pipe.
Process flow chart of two stage gas producer thermal desorption gas:
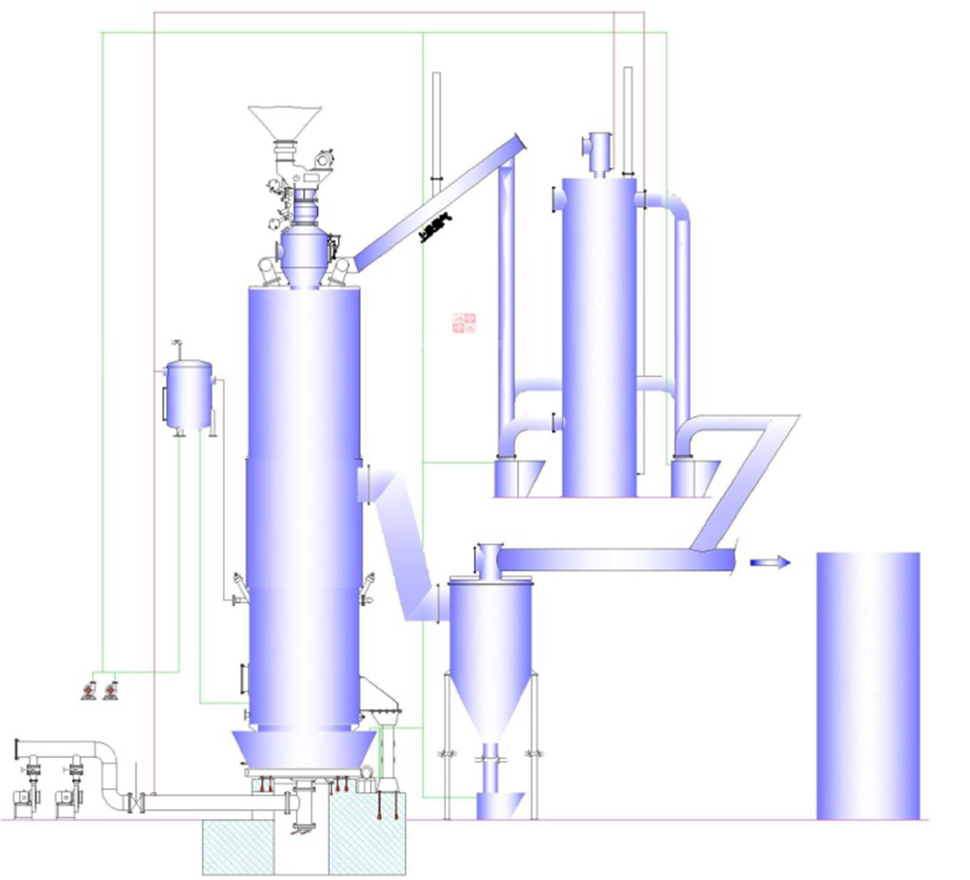
Process flow of cold coal gas station of double-stage coal gasifier:
The coal gas in double-stage can be divided into two kinds, upper gas and lower gas. Upper coal gas enters I grade electric tar precipitator first to eliminate heavy tar and dust. Working temperature is from 90 to 150 degree centigrade. Then, coal gas enter indirect cooler where the temperature of coal gas is cooled to about 35 to 45 degree centigrade. After passing through cyclone dust collector, the temperature of lower coal gas is about 450 to 550 degree centigrade. Then, lower coal gas enters preheat heat ex changer. Gas is recycled while cooling down the gas. The temperature of coal gas is cooled to about 200 to 230 degree centigrade. Then, coal gas enters into air cooling device where the temperature of coal gas drops to about 65 to 80 degree centigrade. Through indirect cooler, the temperature of circulating water drops to about 35 to 45 degree centigrade. After being indirectly cooled, upper coal gas and lower coal gas will enter to secondary electric catcher for further deoiling and dedusting through deoiler. After being cooled and purified, coal gas will be compressed by pressure device. Finally, coal gas will be conveyed and used through coal gas pipes.
Process flow chart of double-section coal gasifier:
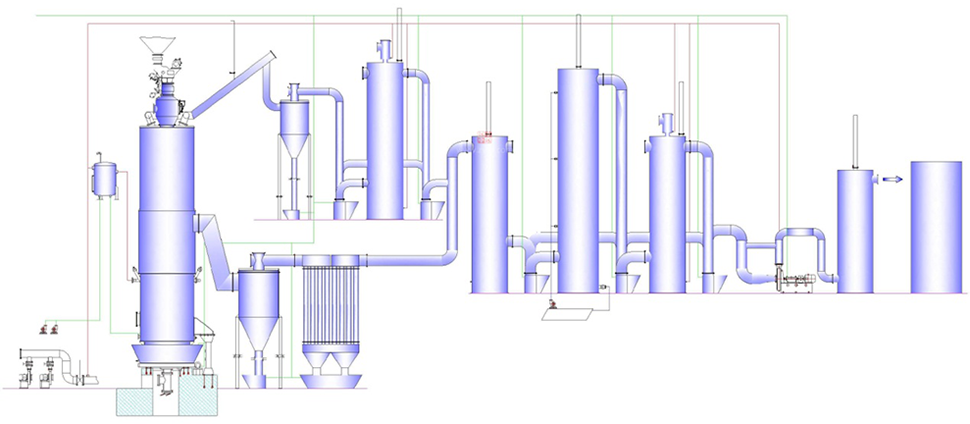
Technical parameters
model parameters | 2.0 | 2.4 | 2.6 | 3.0 | 3.2 | 3.6 |
mm Diameter of furnace | 2000 | 2400 | 2600 | 3000 | 3200 | 3600 |
mm Size of fuel | 13-25、25-50 |
kg/h Fuel consumption | 800-920 | 1200-1400 | 1400-1600 | 2000-2100 | 2100-2500 | 2500-3500 |
m³/h Coal gas output | 2500-3000 | 3600-4200 | 4200-5200 | 6000-6500 | 6500-8000 | 8000-11000 |
KJ/ m³ Thermal value of coal | Upper Part | 7100-7500 | 7100-7500 | 7100-7500 | 7100-7500 | 7100-7500 | 7100-7500 |
Lower part | 5016-5643 | 5016-5643 | 5016-5643 | 5016-5643 | 5016-5643 | 5016-5643 |
Mixing | 6186-6690 | 6186-6690 | 6186-6690 | 6186-6690 | 6186-6690 | 6186-6690 |
℃ Outlet temperature of coal gas | Upper part | 100-150 | 100-150 | 100-150 | 100-150 | 100-150 | 100-150 |
Lower part | 500-600 | 500-600 | 500-600 | 500-600 | 500-600 | 500-600 |
outlet pressure:K Pa | Upper part | <1 |
Lower part | <1.5 |
K pa Air pressure of furnace bottom | 5-6 |
℃ Saturation temperature | 50-65 |
K pa Steam pressure of water jacket | 98/294 |
Kg/h Steam output of water jacket | 300 | 400 | 450 | 500 | 550 | 650 |
r/h Rotary speed of ash basin | 2.97 | 2.3 | 1.7 | 1.5 | 1.5 | 1.5 |
KW Transmission power of ash basin | 3.0 | 4 | 5.5 | 5.5 | 5.5 | 7.5 |
KW Power of hydraulic station | 2.2 |
K pa Gland steam pressure of fire detector | 98/294 |
Fuels available | Non adhesive and weakly bonded bitumite and anthracite; the quality of coal should conform with GB/9143. |
mm Diameter of coal gas outlet | Upper part | DN250 | DN300 | DN300 | DN400 | DN400 | DN600 |
Lower part | 400x400 | 766x766 | 766x766 | 866x866 | 866x866 | 1000x1000 |
Diameter of blast pipe at furnace bottom | DN250 | DN300 | DN300 | DN400 | DN400 | DN600 |
KW Total power | 40 | 55 | 70 | 100 | 150 | 190 |
Slag discharge form | Wet type, automatically discharge slag;
|