TAEDA Hollow Paddle Dryer is a compact and highly efficient indirect heat exchanging and stirring equipment. It is mainly composed of upper cover, rotating shaft, shell (including jacket), frame and driving device. As core component of paddle dryer, rotating shaft is composed of hollow blades and hollow shafts with special flow channels. The main body is installed horizontally (or inclined). Material enters dryer from the front end and shell form a slight inclination angle with horizontal plane and rotating shaft. The product moves to the discharge end relying on its own weight along with rotation of the rotating shaft. At the discharge end, product flows out of the equipment through overflow port and enters the next process. Heat is indirectly transferred to materials through hollow blades of rotating shaft, hollow shaft and heating/cooling medium in the shell jacket so that to achieve drying purpose.
Paddle dryer is mainly used in processes such as drying, reaction, cooling, crystallization, evaporation, heating and disinfection, and low-temperature calcination. It is also suitable for drying various organic and inorganic materials with stable heat sensitivity and heat sensitive materials under vacuum conditions. One machine can fulfill multiple purposes.
According to different heat exchange media, paddle dryer is divided into two types, steam (saturated steam or superheated steam) type and liquid (hot water, heat conduction oil, heat medium, refrigerant, soft cold water or chilled water) type. Paddle dryer can be operated both continuously and intermittently. Heat exchanging medium (steam, heat conduction oil or water) is always separated from product. According to number of rotating shafts, it is divided into single shaft, double shaft and four shaft blades. According to different operating pressure, it is divided into vacuum, normal pressure and positive pressure type.
Drying shafts are relatively meshed and rotated. Special blade structure ensures that heat exchange surfaces on both sides of the hollow blades fully contact with materials so that materials are squeezed and loosen between blade shafts. Heat exchange surface has self-cleaning function. Relative movement between surfaces of the hollow stirring blade and material granules produces a scrubbing effect, which can scrub away the materials attached to blades’ surface so that rotating shaft always maintains a clean heat transfer surface during operation.
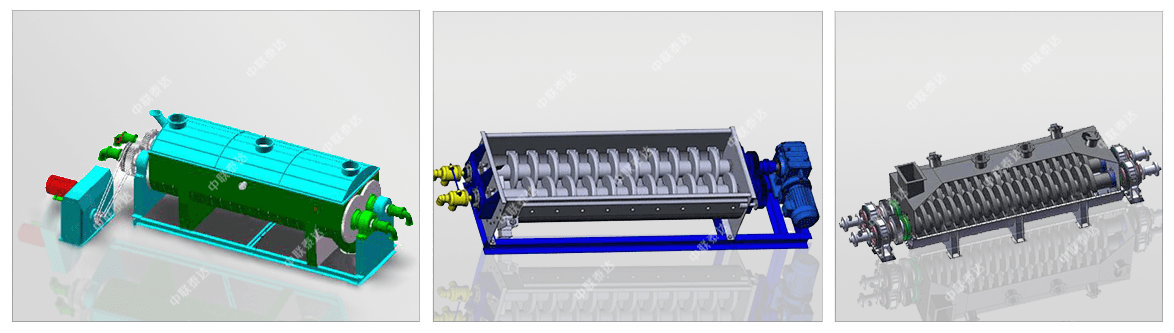
Multiple operation mode:
TAEDA paddle dryer has been successfully used in food, chemical, petrochemical, dye, industrial sludge and other fields. Characteristics of heat transfer, cooling, and stirring of the equipment enable it to complete following unit operations: cooling, drying (solvent recovery), heating (melting), reaction and sterilization. The stirring paddle itself is heat transfer surface, which increases heat transfer area in unit effective volume and shortens processing time. Wedge-shaped paddle heat transfer surface has self-cleaning function. Mixing function makes materials mix evenly. Material moves in a "piston flow" along axial direction. In axial interval, gradient of materials’ temperature, humidity, and mixing degree are very small.
Specifically, it can operate: calcium sulfate dehydrate (Ca2SO4•2H2O) is burned into calcium sulfate hemihydrate (Ca2SO4•1/22H2O); sodium bicarbonate (NaHCO3) is converted into soda ash (Na2HCO3) after calcination. Cooling medium such as water, cooling brine and etc. For example, blade-type alkali cooling machine used in soda ash industry replaces old air-cooled alkali cooling machine, which saves energy consumption, reduces exhaust gas treatment equipment and decreases operating costs. In terms of drying operation, TAEDA paddle dryer does not use hot air, which makes energy consumption and environmental control in an ideal easy handling state. It has been widely used in fine chemical, petrochemical and dye industries.
Applicable material:
◎Petrochemical industry: polyolefin powder, polycarbonate resin, high and low density polyethylene, linear low density polyethylene, polyacetal particles, nylon 6, nylon 66, nylon 12, cellulose acetate, polyphenylene sulfide, propylene Base resin, engineering plastic, polyvinyl chloride, polyvinyl alcohol, polystyrene, polypropylene, polyester, polyoxymethylene, styrene-acrylonitrile copolymer, and ethylene-propylene copolymer.
◎Environmental protection industry: PTA sludge, electroplating sewage sludge, boiler soot, pharmaceutical factory waste residue, sugar factory waste residue, MSG factory waste residue and coal ash.
◎Feed industry: soy sauce residue, bone-based feed, distiller's grains, food scraps, apple pomace, orange peel, soybean meal, chicken bone feed, fish meal, feed additives and biological residue mud.
◎Food industry: starch, cocoa beans, corn kernels, salt, modified starch and medicines.
◎Chemical industry: soda ash, nitrogen, phosphorus and potassium compound fertilizer, kaolin, bentonite, white carbon black, carbon black, phosphogypsum, sodium fluoride oxide, calcium nitrate, magnesium carbonate, sodium cyanide, aluminum hydroxide, barium sulfate, calcium sulfate, Calcium carbonate, dyes, molecular sieves, and saponin.
◎Low energy consumption: Due to indirect heating, there is no large amount of air taking away heat. Outer wall of dryer is equipped with insulation layer. For slurry materials, it only consume 1.2kg of vapor to evaporate 1kg water.
◎Low system cost: Unit effective volume has a huge heat transfer surface, which shortens the processing time and reduces the equipment size. Meanwhile, greatly building area and space are greatly reduced.
◎Wide range of processing materials: Using different heat medium, it can process heat-sensitive materials as well as materials that require high-temperature processing. Commonly used medium are: steam, heat conduction oil, hot water, cooling water and etc. It can be operated both continuously and intermittently. It can be applied for many fields.
◎Less environmental pollution: No carrying air is used and less dust materials are entrained. Evaporation of material solvent is very small, which is easy to handle. For materials which may cause pollution or working conditions that require solvent recovery, closed loop can be used.
◎Low operating cost: Reasonable structure, less abrasion amount and low maintenance cost.
◎Stable operation: Due to compression-expansion and stirring effect of special wedge-shaped paddle, material particles are fully in contact with heat transfer surface. In axial interval, gradient of materials’ temperature, humidity, and mixing degree is small, thereby ensuring the process stability.