Taeda MED series new type sticky material drying system is developed based on MGT rotary drum dryer. It can be widely applied for:
1. coal industry for drying coal slurry, raw coal, lignite, semi-coke, floating clean coal and mixed clean coal;
2. construction industry for drying furnace slag, gypsum, clay, limestone and sticky gypsum;
3. beneficiation industry for drying metal concentrate, tailings, ore slurry and waste slag;
4. chemical industry for drying materials which are not heat sensitive;
5. for drying sludge cake and sticky sludge after industrial waste water and municipal waste water treatment.
Besides, MED dryer can also be used for drying following materials:
◎Large particle materials from chemical industry, mining industry and metallurgy industry; materials with large specific weight like mining slag, furnace slag, coal, metal powder, phosphate fertilizer and ammonium sulphate.
◎For powder and particle materials which need special drying process like HP foaming agent, spent grain residue, light calcium carbonate, active clay, magnetic powder, graphite and medicine residue.
◎Materials which should be dried continuously in large quantity under lower temperature.
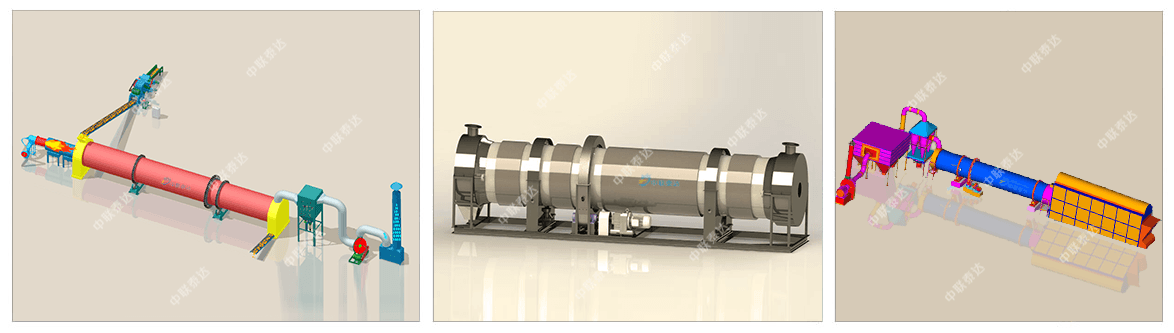
■Designed according to sludge feature; with good performance for drying sludge materials.
■Energy-saving and high efficient: quick drying speed, uniform drying effect, energy saving, high efficient, easy to control, safe and no pollution.
■Automatic and intelligent control: Compared with common dryer, coal consumption, fuel consumption and electricity consumption are 10% to 15% less.
■Exhaust gas purification system can be configured according to facts so that to meet standard emission requirements.
Wet materials are sent to push-floor silo by belt conveyor, screw conveyor and sludge pump. Then, wet materials will enter feeding end through feeding pipe of feeder set under silo. MED drum dryer is a horizontal rotary drum dryer slightly inclined with horizontal line. Materials enter to dryer through higher end and heat carrier enters dryer through lower end. Heat carrier will contact with materials counter-currently. There are also some situations where materials enter dryer with heat medium. Along with the rotation, materials move to lower end under the function of gravity. During the moving forward process, wet materials are directly or indirectly heated by heat medium. In this way, wet materials are dried and dry products will be discharged out by belt conveyor or screw conveyor. There is lifting plates set inside drum. The function of lifting plates is lifting and scattering materials so that to enlarge the contact surface between materials and air flow, improve drying efficiency and drive materials move forward. Heat medium is generally divided into hot air and flue gas. After passing by rotary drum dryer, materials brought by heat carrier shall be caught by cyclone. If dust content in exhaust gas needs to be further reduced, exhaust gas shall pass by bag filter or wet type dust removing machine before discharging to air.
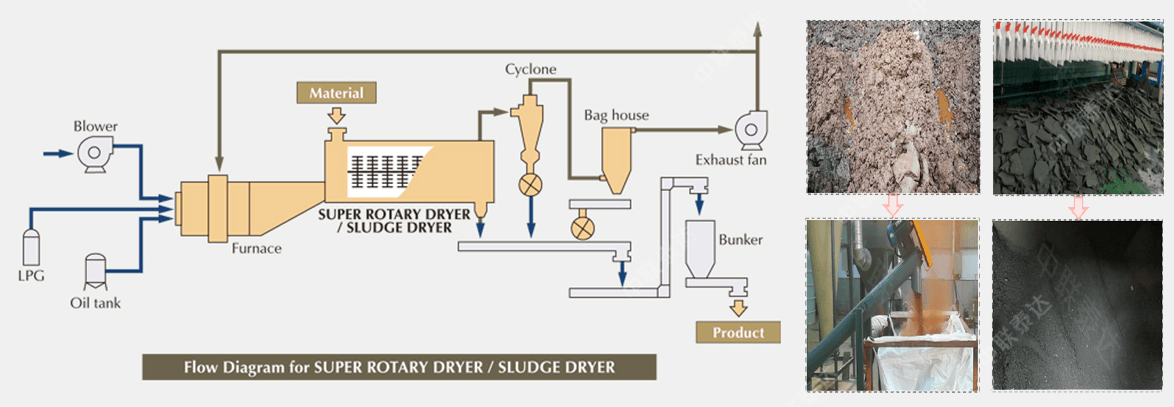
Model |
Slope |
Rpm |
Maximum air inlet temp |
Power |
Capacity |
MED600 |
3-5 |
1-7 |
≤850 |
3 |
Shall be decided according to dryness of raw material and moisture content of final product. |
MED800 |
3-5 |
1-7 |
≤850 |
4 |
MED1000 |
3-5 |
1-7 |
≤850 |
5.5 |
MED1200 |
3-5 |
1-7 |
≤850 |
11 |
MED1500 |
3-5 |
1-7 |
≤850 |
15 |
MED1800 |
3-5 |
1-7 |
≤850 |
18.5 |
MED2000 |
3-5 |
1-7 |
≤850 |
22 |
MED2200 |
3-5 |
1-7 |
≤850 |
30 |
MED2400 |
3-5 |
1-7 |
≤850 |
37 |
MED2600 |
3-5 |
1-7 |
≤850 |
40 |
MED2800 |
3-5 |
1-7 |
≤850 |
55 |
MED3000 |
3-5 |
1-7 |
≤850 |
75 |
MED3200 |
3-5 |
1-7 |
≤850 |
90 |
MED3400 |
3-5 |
1-7 |
≤850 |
110 |
MED3600 |
3-5 |
1-7 |
≤850 |
150 |
MED4000 |
3-5 |
1-7 |
≤850 |
190 |
MED4200 |
3-5 |
1-7 |
≤850 |
200 |
MED4500 |
3-5 |
1-7 |
≤850 |
260 |