RS series coal powder burner developed by our company learns from foreign advanced technologies and design concept. With guidance of relevant experts in national academy of sciences, we develop a new generation of burner according to the quality of coal. This product takes advantage of large of velocity difference principle of the same direction. It makes full use of secondary air, which makes the temperature of coal powder to ignition point. When the coal powder leaves the nozzle, coarse conical flame will be formed. Stable plate technology is adopted in the inner wind which makes the flame reach to best effect. At the same time, the service span of nozzle can be increased. Kiln skin can be protected and the service span of kiln liner can be expanded. The amount of primary air only takes up 5 to 7% of total. It is characterized by energy-saving. For 30% to 35% lignite, about 10% anthracite is volatilized. The emission of exhaust air can be reduced by over 30%.
The structure of four-channel coal powder burner adopts technology of foreign advanced burner. By analyzing problems of three-channel burner faced by many factories at home, we decide the structure of four-channel burner nozzle. The four channels are center wind, swirling wind, coal wind and DC wind channels from inside to outside. An ignition oil gun can be set in center wind channel according to customer’s request. Center wind flows out through small holes distributed on flame stabilizing plate. Flow amount of wind accounts for 0.03% to 0.05% of primary wind. Center wind plays an important role for adjusting negative pressure of jet center re-circulation zone and changing position and size of high temperature zone. Swirling wind channel adopts long helical vane shaft type cyclone. Its special structure can not only reduce aerodynamic resistance, but also can produce enough swirling intensity. With scientific design, it is not easy for these channels to be blocked. For wear parts, ceramics are pasted in order to guarantee the service span. 12 to 16 circuferentially distributed nozzles are installed at DC wind tunnel. With its special cavity design and precise working, these nozzles can produce strong air flow. With less energy loss, these nozzles can improve exit momentum of DC wind and jet flow pattern. In addition, there is a steady flame hood set at external part of DC wind channel in order to avoid early distribution of flame. Meanwhile, it can protect nozzle head.
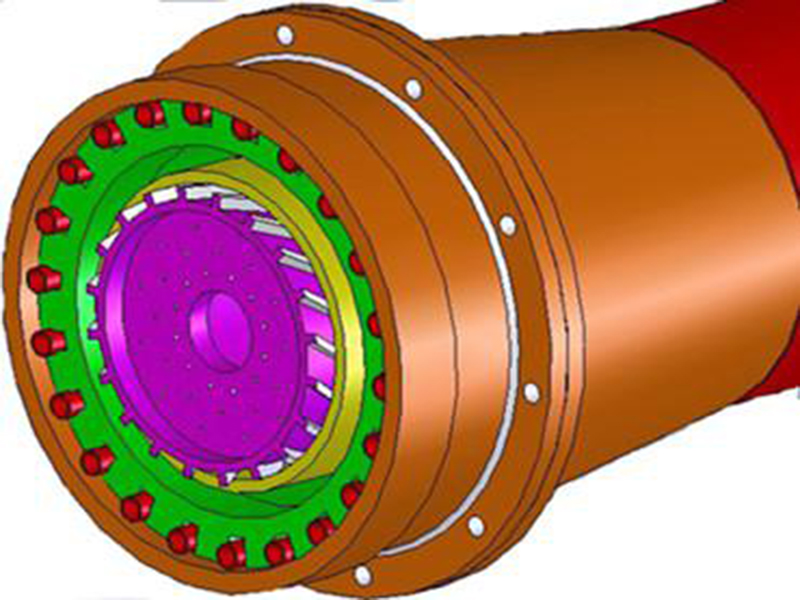
It has been demonstrated by practices and theories that the central disc flame stabilizing device is helpful to form the inner re-circulation zone. The geometry of the exit of the swirl wind has an important effect on the velocity of the jet and the position of the inner re-circulation zone. Under the same swirling intensity, the radial distance between the axial and tangential velocity peaks can be increased with the expansion of the extension port. Four-channel coal powder burner adopts axial telescopic structure for its internal and external casing. It can be adjusted according to real situation in order to produce expansion of nozzle. It is proven by practices that this kind of adjustment is very helpful for controlling the shape of flame.
The product of air flow rate (m, kg/s) and jet velocity of the four-channel coal powder burner is called the thrust of the burner M (N). The mixing speed between secondary hot air and coal powder and combustion speed of coal powder will improve with the increase of burner thrust. However, if the thrust is too high, there will be negative effects produced. Thus, if users want to limit thrust and relative momentum, users must improve the speed of primary air after reducing the speed primary air. According to recommended values, we can estimate that the speed of primary air is about 180 to 220m/s for primary air volume. At present, many three-channel burners can not reach this standard.
The wind speed range of four-channel coal powder burner: DC external wind: 160 to 250m/s; swirling inner wind: 120 to 245m/s; coal wind: 20 to 35m/s. it is demonstrated in industrial practice that the volume of primary air can be effectively reduced by improving exit momentum of primary wind;
Technical features:
1. The shape of flame can be adjusted;
There are many adjustment methods for four-channel coal powder burner. With same air volume, different ratio of inner and external wind and exit jet flow type can be adjusted steplessly in order to get proper flame shapes suitable for various situations.
2. Save energy and reduce consumption:
Owing to small amount of primary wind, DC wind and swirling wind can be adjusted to best ratio, which is beneficial for full combustion of coal powder. It is demonstrated that if every 1% primary air volume is reduced, 8.70 to10.46kJ/kg fuels can be reduced. Meanwhile, secondary air can be improved obviously.
3. Has strong adaptability to coal: can use low-volatile coal and anthracite; the finess (The percentage of 0.080mm sieve residue is 0.5 to 0.75 times of the percentage of volatile) is adjusted according to the volatile content of combustion; meanwhile, adjust the thrust of burner in order to realize the application of low-violate coal for incineration in rotary kiln.
4. Low emission of NO: there is high-temperature flue gas at front part of four-channel burner. The flue gas will flow back which produces a negative pressure zone in order to prevent the occurrence of local high temperature. The curve change of temperature along the kiln is very stable, which can effectively avoid the the combustion of NOX and high-temperature NOX. The amount of NOX can be reduced by about 20% to 30%. The emission of flue gas meets national standard.
5. Reasonable structure and good performance: four-channel coal powder burner is characterized by beautiful appearance, complete equipment, small resistance, flexible adjustment and simple maintenance, the performance of this equipment can reach the advanced level of foreign countries.
6. New technology and new materials guarantee long service span: special wear-resistant spraying technology is adopted for vulnerable parts of four-channel coal powder burner. Wearing life of key parts of burner is improved by 5 to 10 times than that of normal steel. Front part and nozzle of four-channel coal powder burner adopt heat-resistant steel, which can guarantee two-year service span under 1100 degree centigrade.
7. Flexible positioning and adjustment:
Suspension system of four-channel coal powder burner can extend and turn according to demand of working conditions in order to produce expansion effect for nozzle.
For burner of small-sized kiln, our company has broken through successfully. Low installed capacity: rotary kiln with daily production of 150 tons; two root blower: total installed capacity is 26.5 kW. Many factoried can produce large equipment but has difficulties to produce burners for small-sized kilns, because the production, process and size demands are higher and more complex. What’s more, the requests for feeding, insulation and operability are higher. Our company adopts aurora location and NC machining nozzle, which has basically meet relevant requirements.