Technical introduction
Production introduction:
Colter mixer can dispose mixture of solid powde and granular materials. It is suitable for batching mixing project which needs add liquid. It has been widely applied to food, chemistry and building materials. It is especially applied to food additives, ready-mixed mortar, composting technology, sludge disposal, rubber plastics and special building materials. Strong cutting action makes it with good mixing quality.
Total volume of equipment: 0.3 to 30 cubic meters
Processing capacity of each batch: 0.1 to 20 cubic meters
Materials amount processed each batch: 0.3 to 15 tons
Mixing time: 3 to15 minutes
Power for driving device: 3 kw to 160 kw
The texture of equipment can be divided into 316L, 321, 304 and carbon steel.
Advantages
Performance introduction:
1.Flexible material selection scheme 2. Reliable driving device
Mixer is made from carbon steel, manganese, 304 stainless steel, 321 stainless steel and other steel materials. Different materials can be used as a combination. While select materials for equipment: the part which contacts with materials and the part which doesn’t contact with materials;
Coatings and protection layer which holds function such as corrosion resistance, anti adhesion, separation and wearproof can be added inner mixer. The disposal methods for the surface of stainless steel are classified into sand blast, drawbench, polishing and mirror. These diposal methods can be used for different parts.
2. Reliable driving device
According to different quality, starting method, mixing method, the mixer can arrange cutomized drive device with different capacity, power and different rotary speed. The driving motor can be divided into: normal motor, explosion-proof motor, converter motor, efficient and energy-saving motor, high protection grade motor and motor under different voltage; common reducer motor: R,K, F gear reducer, cycloidal pin wheel reducer, universal gear box, planetary gear reducer; common connection methods: direct coupling, belt pulley connection and hydraulic coupler connection.
3. Efficient agitating device
Plough type cutting head can be detachable in colter mixer, which can achieve quick change effect; colter will get wear resistant treatment, so it is more suitable for relatively fast wear condition. According to different qualities of materials, different agitators can be selected for mixer.
The spindle agitator: general coulter, sawtooth coulter, scrapor razor, high speed flying shear, multi blade knife and double leaf lotus knife;
4. Good discharger device
Horizontal colter mixer is generally configured with curve surface turning valve. The curve surface turning plate fits with the cylinder surface completely. In the process of agitating, there is no additional agitating dead angle, which makes the mixing of materials more even. The driving of valve can be divided into three kinds, manual, pneumatic and electrical driving modes.
There are other valves for your reference powder ball valve, cylinder valve, plum blossom valve, powder butterfly valve and rotary feeding valve.
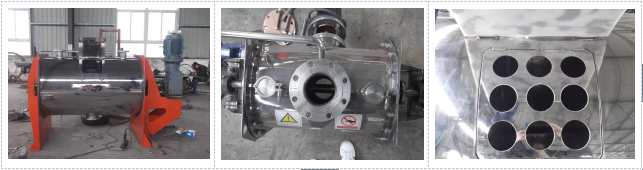
5. Strong auxiliary components
Many components can be added to mixer. There are some common components used, coil steam jacket, honeycomb pressure jacket, circulating media jacket, one-line sampling valve, high speed fly knife, high temperature probe, weighing system, dust wiper and purification components. According to different media of heat source, there are several forms of jackets which can be chosen. the temperature can be increased and also can be cooled. The higest temperature can be controlled within 250 degree centigrade.
While add a little amount of liquid, spray liquid sraying device is needed, which makes liquid evenly scatter and mix in the main materials.
Liquid injection system is composed of pressure source, fluid reservoir and nozzle.
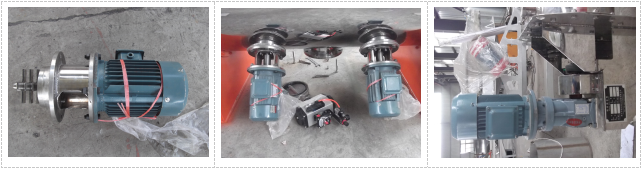
6. Tight dynamic shaft seal
There are three kinds of sealing modes, packing seal, combined gas seal and mechanical seal; it is used to handling main shaft seal problem of granular, powder, micropowder, liquid and sizing agent.
There are other valves for your reference powder ball valve, cylinder valve, plum blossom valve, powder butterfly valve and rotary feeding valve.
Working principle
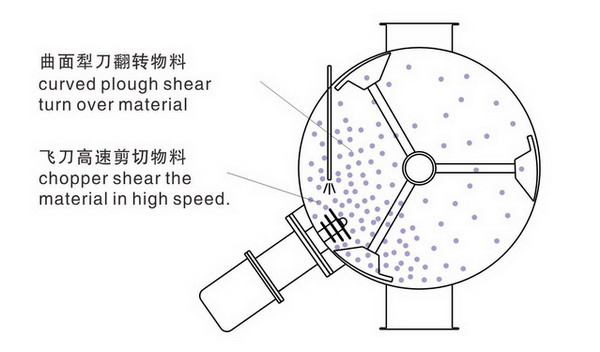
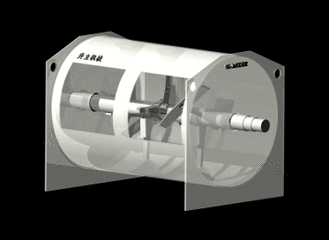
Colter mixer is a kind of single-shaft forced mixing equipment. There are many groups of colter agitators which are installed in a misplaced and continous way. Agitating dead angle can be avoided in the structure. In the process of running, different intermittent centrifugal force is produced. Misplaced colter constantly agitates and spiral centrifugal material flow constantly overlaps and disperses which makes materials boil and form convective circulation which will agitate materials rapidly.
Pellet materials such as fiber and powder with liquid condensation. By using the fast flying knife installed at colter mixer and combining with the convection circulation which will disperse and separate pellet materials.
High-speed fly knife is installed on the ploughshare mixer cylinder side down 45 degrees. The head of knife will extend to drum; in the process of agitating, materials are driven by colter to a effective range where fly knife can reach and carry out high-speed shearing.
Technical parameters
Parameters of selection
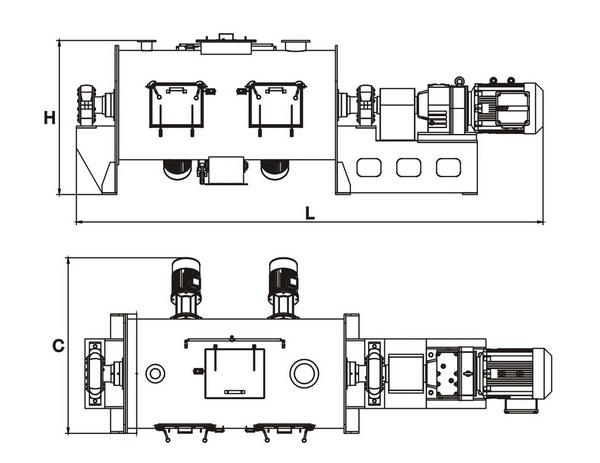
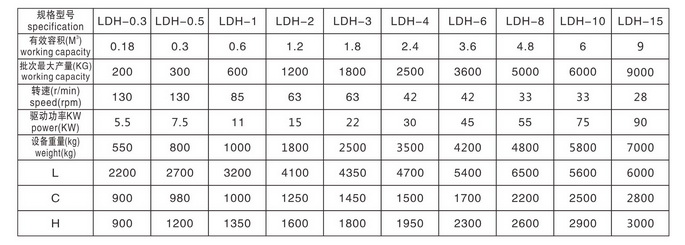
Selection methods
1. Make sure that volume of materials used for mixing; the range is controlled between 0.1 square meters to 20 square meters. Select proper equipment according to real situation.
2. Select proper materials for equipment; textures are divided into two parts, the part which contacts with materials and the part whic doesn’t contact with materials. The other part of equipment will maintain the original texture.
According to quality, working demands and health level requirement, the texture can be divided into carbon steel, 304/316L/321 stainless steel;
After the selection of materials,decide the surface disposal requests according to specific requests;
3. According to the proportion of materials, mobility and start-up standard, decide the drive ability configured. Types of start-up standard:
Heavy load start-up; non-load starting;
4. According to real process requests, add auxiliary function components such as hydroject, heating/cooling and etc.
5. The requests for the design of device opening such as feeder, charging hole, cleaning port and vent hole;
6. Choose discharging mode and drive mode: it can be divided into manual mode, pneumatic mode and electrical mode;
Note: the selection of equipment is a very important part. Customers are supposed to provide detailed information of materials and process arrangement in order for that we can offer best services.
Matched plan
Configuration 1: use tons bags raw materials; crane hoisting; directly feed combines with dust wiper;
Configuration 2: build multi-layer platforms; manual diasssembly feeding; after mixing the materials, adopt ton-bag packing machine;
Configuration 3: it is the easiest mixing equipment; direct feed and direct discharge; forklift is set to dicharge and load materials;
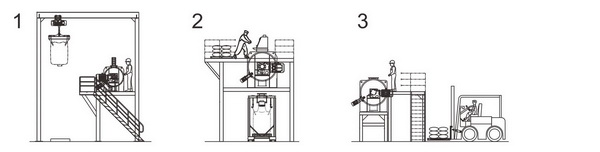
Configuration 1: use manual feeder platform; after mixing, materials are sentto finished product bin by screw. it connects with packing machine at the bottom part;
Configuration 2: adopt vacumm feed method; ground feed; after mixing, adopt ton-bag packing machine;
Configuration 3: multilayer vacumm feed conveyer; after mixng and storing, packing is carried out.
Configuration 1: multilayer opertion platform design; use ladder to convey, feed, store, mix and pack; whole tower structure;
Configuration 2: adopt bucket elevator to convey materials; then mix, store and pack;
Configuration 3: vacumm feeder to feed, mix, store and pack; whole structure of upper and lower part;
Configuration 4: manully feed, mixing, store and pack; whole structure of upper and lower part;