Technical introduction
Product introduction:
Double-screw cone mixer is widely applied to chemistry, pesticide, dyestuff, food, battery materials, rare earth and other powder materials;
1. It holds high standard requests so there is no residue after discharging;
2. Soft agitating mode which will not damage brittle materials such as crystal materials;
3. Low energy consumption; mixing effect can well adapt to physical and chemical reaction.
Total equipment volume: 0.3 to 30 cubic meters
Mixing time: 15 t0 60 minutes
Power for drive unit: 1.5 kw to 55 kw
Texture of equipment can be 316L, 321,304 and carbon steel.
Selection mode:
Selection methods
1. Make sure that volume of materials used for mixing; the range is controlled between 0.1 square meters to 20 square meters. Select proper equipment according to real situation.
2. Select proper materials for equipment; textures are divided into two parts, the part which contacts with materials and the part which doesn’t contact with materials. The other part of equipment will maintain the original texture.
According to quality, working demands and health level requirement, the texture can be divided into carbon steel, 304/316L/321 stainless steel;
After the selection of materials,decide the surface disposal requests according to specific requests;
3. According to the proportion of materials, mobility and start-up standard, decide the drive ability configured. Types of start-up standard:
Heavy load start-up; non-load starting;
4. According to real process requests, add auxiliary function components such as hydroject, heating/cooling and etc.
5. The requests for the design of device opening such as feeder, charging hole, cleaning port and vent hole;
6. Choose discharging mode and drive mode: it can be divided into manual mode, pneumatic mode and electrical mode;
Note: the selection of equipment is a very important part. Customers are supposed to provide detailed information of materials and process arrangement in order for that we can offer best services.
Advantages
1. Flexible material selection scheme:
Mixer is made from carbon steel, manganese, 304 stainless steel, 321 stainless steel and other steel materials. Different materials can be used as a combination. While select materials for equipment: the part which contacts with materials and the part which doesn’t contact with materials;
Coatings and protection la
yer which holds function such as corrosion resistance, anti adhesion, separation and wear-proof can be added inner mixer. The disposal methods for the surface of stainless steel are classified into sand blast, draw bench, polishing and mirror. These disposal methods can be used for different parts.
on and wearproof can be added inner mixer. The disposal methods for the surface of stainless steel are classified into sand blast, drawbench, polishing and mirror. These diposal methods can be used for different parts.
Power of drive configuration: 3 kw to 150 kw
Materials of equipment can be classified into 316L, 321,304 and carbon steel.
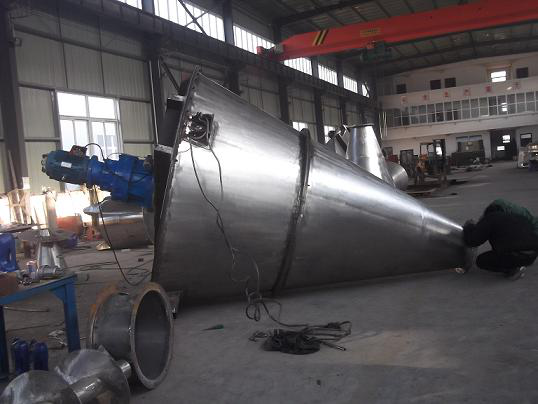
2. Reliable drive device
According to the quality of materials, start-up mode and process requests, it adopts different drive device with different powers and different capacities.
Special double-output speed reducer used for double-screw cone mixer on load adopts various forms such as pin gear, cyclonic-pin wheel, gear and combination of worm and gear.
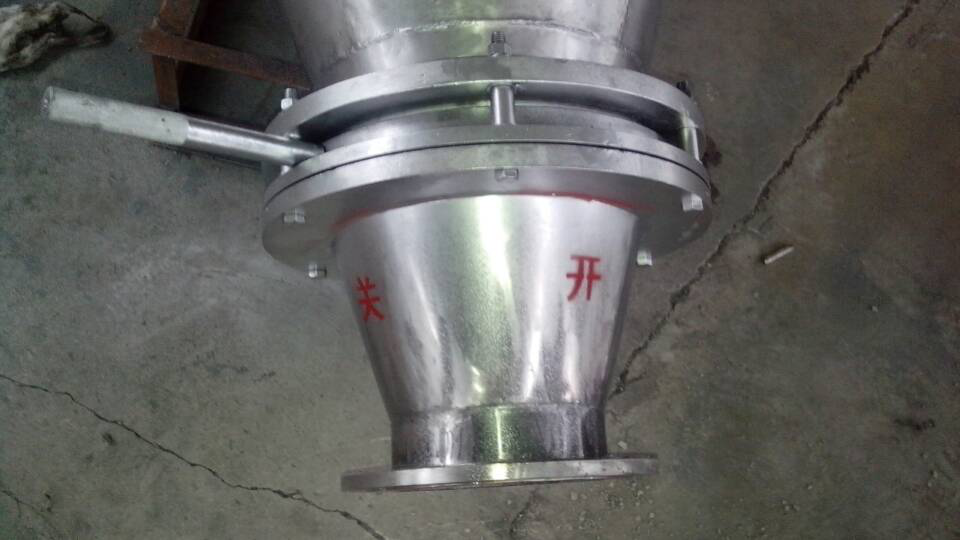
3. Double-screw cone mixer is equipped with powder ball valve or plum blossom valve; raised sphere of powder ball valve will move fitting with the bottom sphere of screw, which can farthest reduce agitating dead angle and realize largest area of discharging port in order to guarantee the discharge of material residues. Ball valve holds great sealing performance for powder, liquid and negative pressure state. The plum blossom dislocation valve can realize simple operation and control discharge speed. It can even combine with long spiral bottom supporting device. The valve drive can be divided into three kinds, manual, pneumatic and electrical kinds.
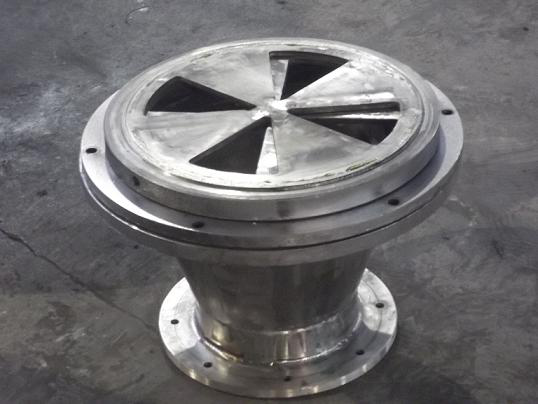
4. Strong auxiliary components
Double-screw cone mixer can be equipped with circulating jacket or steam coil jacket to realize temperature controlling as agitate materials;
The contact surface between drum and materials can optimize performance of anti corrosion, anti adhesion and coating of metal separation. Agitating screw can build up wear-resistant alloy, so it is suitable for working conditions where there are much abrasion. While add a little amount liquid, liquid and atomizing device is needed to configured, which is better for that liquid scatter and mix in materials. Liquid injection system is basically composed of pressure source, liquid tank and nozzle.
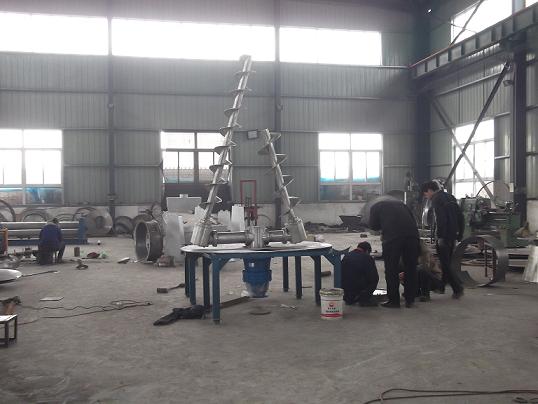
Working principle
When double-screw cone mixer relys on two asymmetrical screws of inner cantilevers which revolve on its own around its own axis, double-screw cone mixer is driven by cantilever and forms orbital revolution around the central shaft of drum.
Double-screw cone mixer can form four action force of four directions.
1. Two asymmetrical shafts rotates on its own and lift materials upward;
2. Cantilever slow revolution around its drum makes materials move circularly.
3. Two revolutions cooperate with each other; materials will be absorbed by the rotation of screw. At the same time, materials will spread towards different directions;
4. Two groups of material flow elevated to upper part will converge towards center; then, a downward of flow direction of the center will be formed to supply the vacancy zone at the bottom; therefore, a integrated circulation slow will be formed.
Technical parameters
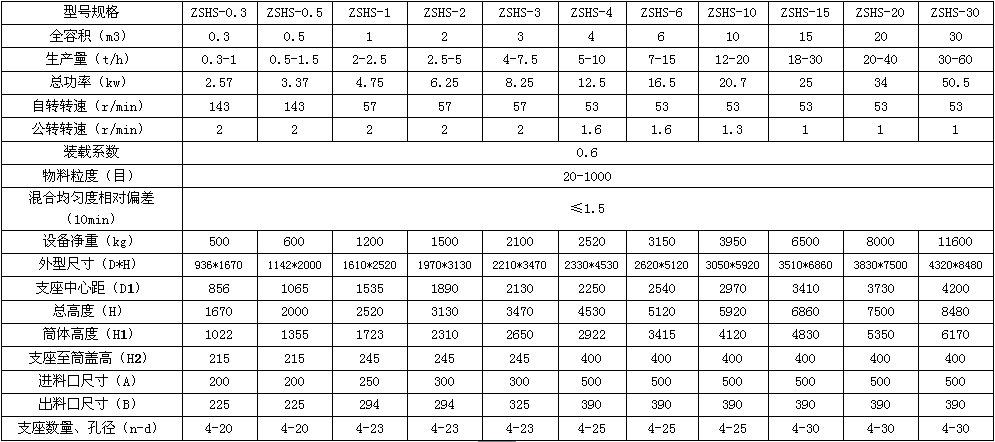
Matched plans
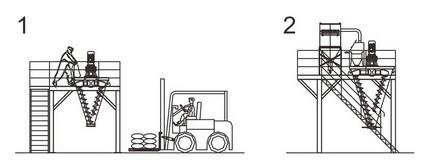
Configuration 1: simple operation platform; operate with the cooperation of forklift;
Configuration 2: platform structure; combines with no-dust feeding system; clean operation;
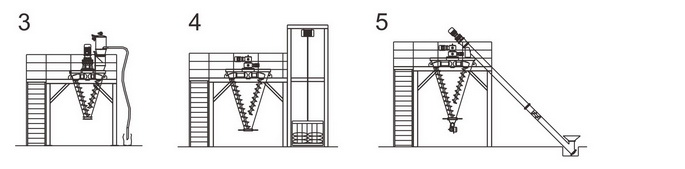
Configuration 1: cone mixer combines with bucket elevator and automatic packing machine forms a simple production process;
Configuration 2: build multi-la
yer platforms; manual dis-assembly and feeding; vacuum feeding; finished products storage; automatic packaging;
Configuration 3: cone mixer build up platform; manually feeding; elevate materials secondary into finished products bunker; then, start package;
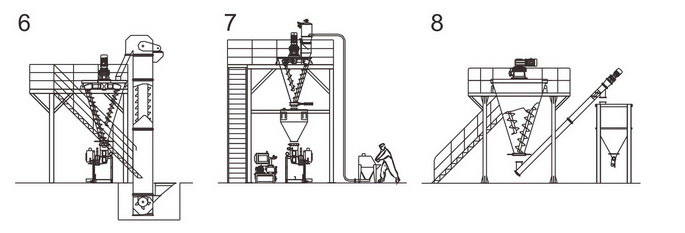
Configuration 1: cone mixer combines with bucket elevator and automatic packing machine forms a simple production process;
Configuration 2: build multi-layer platforms; manual dis-assembly and feeding; vacuum feeding; finished products storage; automatic packaging;
Configuration 3: cone mixer build up platform; manually feeding; elevate materials secondary into finished products bunker; then, start package;