Selection of dehydrator in sludge disposal process
Author: Taida machine Release time:2016-08-17
Reading guidance:Belt dehydrator, centrifugal dehydrator and plateframe type filter press holds different characteristics. During designing and running, we should choose proper dehydration methods according to many rea
Belt dehydrator, centrifugal dehydrator and plate&frame type filter press holds different characteristics. During designing and running, we should choose proper dehydration methods according to many real factor, such as moisture content, energy consumption, investment, occupation, adaptability and daily maintenance.
1. Belt filter press dehydrator: moisture content of sludge discharged: 68% to 80%; in order to increase sludge dehydration performance, improve sludge cakes’ quality and increase permeability of materials, sludge needs chemical disposal which has a high request on flocculation effects. Running state and quality of sludge discharged are mainly affected by the quality of sludge. About 0.8 kw/cubic meters power is consumed for one cubic meter sludge. The noise during running process is about 70 to 75 db. After long-time running, filter cloth needs maintenance. Generally, two turns needs to be arranged. In running process, high pressure should be used constantly to wash filter surface. Because equipment can not achieve fully closed, there existing gas and water leaking problems in workshops. Running environment is not very sound. Belt filter press enters Chinese market early, so the technology is mature and reliable. The cost for initial equipment investment and maintenance of filter cloth are low. It covers a large area and has certain request for workshop’s environment. Feeding may not be uniform, which causes uneven loading of filter belt. Accordingly, filter belt may deviate. Thus, it requires rich experience of operator.
2. Centrifugal dehydrator: moisture content of sludge discharged is 60% to 85%. In the centrifugal machine, even fine sludge can separate from water. Therefore, just a little amount of flocculant agent is needed. About 1kw/cubic meters power is consumed for one cubic meter sludge. Noise in the running process is 85 db. This machine covers a small area. During dehydration process, it is a constant, closed and automatic work condition, so there is no blockage phenomenon. No need of high pressure to wash inner side of machine. Thus, production efficiency is very high. Discharge screw stoker only needs to be repaired in each three years. Sludge which needs to be disposed is conveyed in the machine constantly. Clear liquor and dehydrated sludge are discharged constantly. Conveying is a automatic process, which greatly reduces labor force intensity. Because there is no belt filter press factory in urban sewage disposal plants, the application of belt filter has a short history. Large filter needs to be imported. Initial investment and maintenance cost are very high.
3. Plate&frame filter press: moisture content reaches to about 65%. Can adapt to various materials. It is suitable for many small-medium sized sludge dehydration plants. Low investment cost; shortcomings: blockage; filter cakes are difficult to take out; can not run constantly; small process capacity; low working pressure; texture of the machine can not afford high pressure; plates are easy to be broken; large consumption of filter cloth; operator is need to be on duty; filter cloth needs be be cleaned manually. The weight and volume of the machine are large; large occupation; bad operation environment;
actories and engineers are trying to reduce the moisture content of sludge and running and operation cost in order to get good disposal effects.
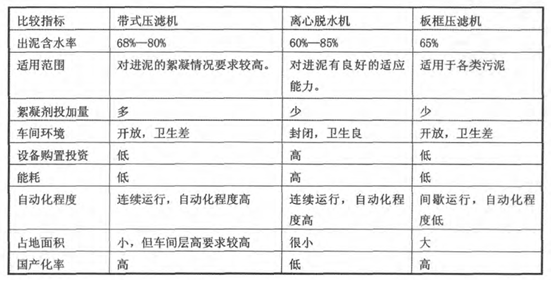
To sum up, the performance of sludge dehydration machines iare shown in the table above: in the selection of urban sewage treatment plant sludge dehydration machine, belt type filter press for the most extensive, the actual market share is the highest. In the design of decision-making in sewage treatment project, can choose the belt filter press to reduce the engineering investment. The centrifugal dehydration machine because of the high cost of investment and operation, generally only used in is not sensitive to the investment, and the mud quality reliability requirement for high sludge treatment and continuous operation, there are strict requirements on engineering workshop sanitation. Filter press has been rarely used in the domestic large quantity of waste water plant, suitable for sludge physicochemical properties is poor, it is difficult to to ensure that the solid content of the mud belt type filter press, and the limited investment projects.
After comparing the band type filter press and a centrifugal dehydration machine, in order to make the sludge water rate is reduced to below 80%, the centrifugal dehydration machine in sludge dehydration industry, municipal sewage treatment plant sludge dehydration is more high-end products, use less frequency. Belt type filter press in sludge dehydration industry is more popular, more commonly used. Centrifugal dehydration machine in the environment, operation management, covers an area of and other advantages. With sludge treatment technology introduction and absorption, equipment localization rate will continue to improve, in future sludge processing field, centrifugal dehydration machine will be more and more big market.
1. Belt filter press dehydrator: moisture content of sludge discharged: 68% to 80%; in order to increase sludge dehydration performance, improve sludge cakes’ quality and increase permeability of materials, sludge needs chemical disposal which has a high request on flocculation effects. Running state and quality of sludge discharged are mainly affected by the quality of sludge. About 0.8 kw/cubic meters power is consumed for one cubic meter sludge. The noise during running process is about 70 to 75 db. After long-time running, filter cloth needs maintenance. Generally, two turns needs to be arranged. In running process, high pressure should be used constantly to wash filter surface. Because equipment can not achieve fully closed, there existing gas and water leaking problems in workshops. Running environment is not very sound. Belt filter press enters Chinese market early, so the technology is mature and reliable. The cost for initial equipment investment and maintenance of filter cloth are low. It covers a large area and has certain request for workshop’s environment. Feeding may not be uniform, which causes uneven loading of filter belt. Accordingly, filter belt may deviate. Thus, it requires rich experience of operator.
2. Centrifugal dehydrator: moisture content of sludge discharged is 60% to 85%. In the centrifugal machine, even fine sludge can separate from water. Therefore, just a little amount of flocculant agent is needed. About 1kw/cubic meters power is consumed for one cubic meter sludge. Noise in the running process is 85 db. This machine covers a small area. During dehydration process, it is a constant, closed and automatic work condition, so there is no blockage phenomenon. No need of high pressure to wash inner side of machine. Thus, production efficiency is very high. Discharge screw stoker only needs to be repaired in each three years. Sludge which needs to be disposed is conveyed in the machine constantly. Clear liquor and dehydrated sludge are discharged constantly. Conveying is a automatic process, which greatly reduces labor force intensity. Because there is no belt filter press factory in urban sewage disposal plants, the application of belt filter has a short history. Large filter needs to be imported. Initial investment and maintenance cost are very high.
3. Plate&frame filter press: moisture content reaches to about 65%. Can adapt to various materials. It is suitable for many small-medium sized sludge dehydration plants. Low investment cost; shortcomings: blockage; filter cakes are difficult to take out; can not run constantly; small process capacity; low working pressure; texture of the machine can not afford high pressure; plates are easy to be broken; large consumption of filter cloth; operator is need to be on duty; filter cloth needs be be cleaned manually. The weight and volume of the machine are large; large occupation; bad operation environment;
actories and engineers are trying to reduce the moisture content of sludge and running and operation cost in order to get good disposal effects.
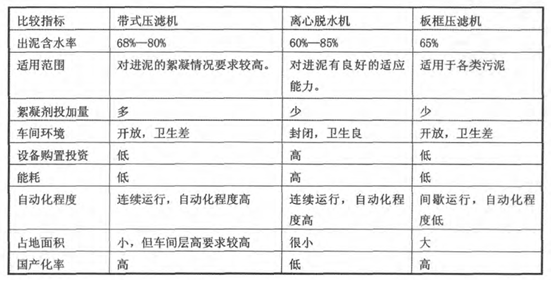
To sum up, the performance of sludge dehydration machines iare shown in the table above: in the selection of urban sewage treatment plant sludge dehydration machine, belt type filter press for the most extensive, the actual market share is the highest. In the design of decision-making in sewage treatment project, can choose the belt filter press to reduce the engineering investment. The centrifugal dehydration machine because of the high cost of investment and operation, generally only used in is not sensitive to the investment, and the mud quality reliability requirement for high sludge treatment and continuous operation, there are strict requirements on engineering workshop sanitation. Filter press has been rarely used in the domestic large quantity of waste water plant, suitable for sludge physicochemical properties is poor, it is difficult to to ensure that the solid content of the mud belt type filter press, and the limited investment projects.
After comparing the band type filter press and a centrifugal dehydration machine, in order to make the sludge water rate is reduced to below 80%, the centrifugal dehydration machine in sludge dehydration industry, municipal sewage treatment plant sludge dehydration is more high-end products, use less frequency. Belt type filter press in sludge dehydration industry is more popular, more commonly used. Centrifugal dehydration machine in the environment, operation management, covers an area of and other advantages. With sludge treatment technology introduction and absorption, equipment localization rate will continue to improve, in future sludge processing field, centrifugal dehydration machine will be more and more big market.
:Analysis of new disposal methods and technology for sludge :Three unification should be achieved in sludge disposal industry
Relevant news
- 2016-01-12OSC-II Model Sludge Dryer Deliv
- 2016-01-1215T/Day Aerobic Dynamic Ferment
- 2016-01-12Matters Should Be Paid Attentio
- 2016-01-12Methods exploration of chemical
- 2016-01-12Analysis of circulating fluid b
Industry trends
- 2016-01-12Comparison Between Different Sl
- 2016-01-12Adding Calcium and Stable Dispo
- 2016-01-12Sludge Treatment: Methods for S
- 2016-01-12Use Dyeing Sludge As Resource
- 2016-01-12Current situation of sludge dis
Hot spots
Hot-sale products
- Leather Industry Sludge Drying
Production Capacity:1-2200t/h
- Welding Plating Sludge Drying S
Production Capacity:1-2200t/h
- Municipal Sludge Drying Solutio
Production Capacity:1-2200t/h
- Manure Sludge Drying Solution
Production Capacity:1-2200t/h